Helicopters attract a whole lot of attention with their almost magical ability to hover, fly in any direction, and operate without runways. They also help save many lives, often in dramatic ways, through their frequent use in all-weather military operations, medical transport, and search-and-rescue missions.
When something goes mistaken, dramatic images and news of helicopter accidents attract public attention. This is particularly true when high-profile Celebrities or Government officials be involved.
However, modern helicopters are secure. Each 12 months, the U.S. industrial helicopter industry completes roughly 3 million flight hours. There have been 0.77 fatal accidents per 100,000 flight hours on average from 2018 to 2022. In comparison, general aviation, which refers to small fixed-wing aircraft and never jetliners, averaged 0.88 fatal accidents per 100,000 flight hours In the identical period.
As an aeronautical engineer, specialized in rotary wing aircraft and director of a National Competence Center for Vertical LiftsI even have observed the efforts of universities, governments and industry to enhance helicopter safety. Numerous technology and training has been invested in helicopter safety.
The long road to safety
Rotary wing aircraft were developed first over a century ago. The first aircraft to be mass-produced was the autogyro, developed by Juan de la Cierva in Spain in 1923. The pinwheel-like structure of the predominant rotor prevented the danger of stall, which was the undoing of so many fixed-wing aircraft on the time. A stall occurs when the angle of an aircraft's wings is simply too great in relation to the airflow, causing the aircraft to lose lift.
Within 15 years, the primary true powered-rotor helicopters – able to hovering, flying slowly, and safely descending within the event of engine failure – were within the air in each Europe and the United States. Large-scale military and industrial production began just a number of years later during World War II.
Today's helicopter operations are based on three predominant principles: comprehensive aircraft design, testing and manufacturing, well-trained flight crews and thorough maintenance practices. Advanced technology plays a critical role in each of those pillars of helicopter safety.
Security basics
Helicopter safety begins with the elemental ability of large-diameter rotors to robotically spin within the event of an engine failure. With the engine off, the rotors spin freely, slowing the helicopter's descent and allowing a controlled landing like a parachute. Reliable powertrains – engines, transmissions and drive shafts – durable rotor blades and low-vibration airframes have also paved the way in which for safer flights.
In addition, modern helicopters are equipped with advanced autopilots and computer-controlled or -assisted flight controls, terrain avoidance radar, and rotor blade de-icing systems that enable all-weather flight. Decades of basic and applied research in university, government, and industry labs have produced many advanced technologies. Today's helicopters typically have radar- and lidar-based collision avoidance systems, comprehensive digital terrain mapping databases, and adaptive controls that help the pilot sense differences depending on flight conditions and aircraft characteristics comparable to payload.
Special pilot training is required to master rotary-wing aircraft. Pilots often train on fixed-wing aircraft before moving on to rotary-wing aircraft, very like you learn to ride a bicycle before venturing onto a unicycle. Pilots spend many additional hours and even years on flight instruction to acquire a helicopter license.
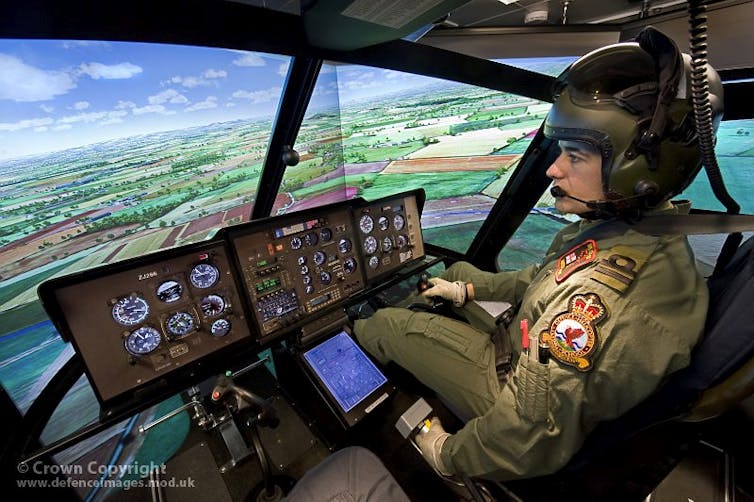
Defense Images/Flickr, CC BY-NC-ND
Rotorcraft inherently have more moving parts than fixed-wing aircraft, making careful design of bearings, gears, shock absorbers, lubrication systems and other mechanical components critical. Like pilots, helicopter mechanics require additional training hours and skills.
In some complex military and rescue missions, mechanics actually fly as integral members of the flight crew. These flight mechanics closely monitor critical systems using onboard temperature, vibration, noise and metal chip sensors and might even troubleshoot many mechanical, electrical and digital problems that arise.
Modern sensors and computer software make helicopter maintenance faster and more thorough. In addition, modern design and manufacturing methods for robust composite materials and special flexible polymers have significantly improved the sturdiness of dynamic components comparable to rotor blades and rotors.
Risks remain
Despite the latest design, training and technology, accidents still occur. In the overwhelming majority of cases, it’s a fancy chain of events. Pilot or mechanical faulttypically related to unusual circumstances, is a significant explanation for many accidents.
Bad Weather often contributes to. Many critical flight operations comparable to search and rescue, firefighting and military transport inevitably happen in sandy, snowy, smoky or stormy environments. These “edge conditions” increase the danger factor despite the most effective technology and training doctrines. Even the extraordinary and realistic training exercises for these missions might be inherently more dangerous than standard flights.
Advanced technologies
New technologies are further improving flight safety in these difficult conditions. These include simpler, reliable and energy-efficient rotor blade de-icing systems, improved weather forecast models and even integrated ice cloud detection systems. Researchers are developing expert systems based on artificial intelligence to assist pilots determine if and when a flight is secure.
I expect that modern technologies will result in further improvements in reliability and safety, in addition to decreasing operating costs, as 1000’s of space engineers all over the world work on life-saving, time-saving and safety-enhancing improvements to those remarkable vehicles.
image credit : theconversation.com
Leave a Reply